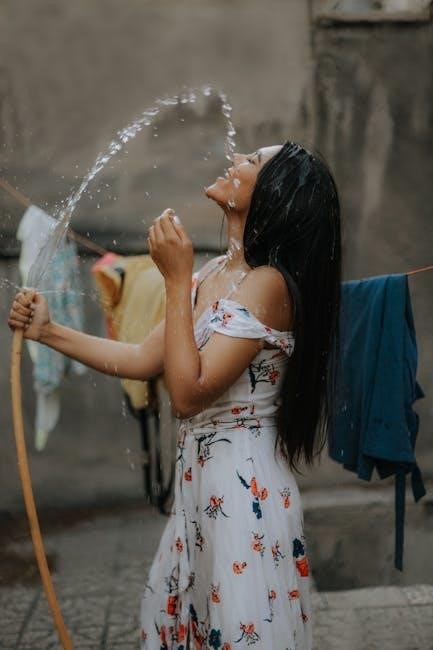
hose guides
Hose guides are essential components designed to direct and control hoses in various systems, ensuring proper alignment and preventing damage. They are crucial for maintaining efficiency and safety.
1.1 Definition and Purpose
Hose guides are mechanical components designed to securely position and direct hoses in various systems. Their primary purpose is to prevent hose kinking, abrasion, and damage while ensuring proper fluid or gas flow. Typically made from durable materials like metals or plastics, they are engineered to withstand harsh environments and heavy usage. By maintaining hose alignment, they enhance system efficiency, reduce wear and tear, and promote safety in industrial, agricultural, and automotive applications. Their versatility makes them indispensable in fluid transfer and control systems worldwide.
1.2 Importance in Various Industries
Hose guides play a critical role across multiple industries, ensuring hoses operate efficiently and safely. In industrial settings, they prevent damage from heavy machinery and harsh conditions. Agricultural equipment relies on them to maintain proper fluid flow during farming operations. Firefighting systems depend on hose guides for quick, reliable deployment, while automotive systems use them to protect hoses from heat and abrasion. Their universal application highlights their essential role in maintaining operational integrity and safety across diverse sectors.
Types of Hose Guides
Hose guides are categorized into fixed, adjustable, and retractable types, each designed for specific applications to ensure proper hose alignment, reduce wear, and enhance system performance.
2.1 Fixed Hose Guides
Fixed hose guides are stationary components designed to hold hoses in a permanent position, ensuring proper alignment and minimizing movement. They are ideal for applications where hoses do not require flexibility or frequent repositioning. Typically made from durable materials like metal or rigid plastics, these guides provide long-lasting support and protection against abrasion. Commonly used in industrial machinery and automotive systems, fixed hose guides are simple, cost-effective solutions for maintaining hose integrity and preventing misalignment. Their robust design ensures reliability in high-stress environments, making them a popular choice for static or permanent installations.
2.2 Adjustable Hose Guides
Adjustable hose guides are versatile components designed to accommodate varying hose positions and angles. They allow for customization and repositioning, making them ideal for dynamic applications. Commonly used in automotive and industrial settings, these guides reduce wear and tear from friction and misalignment. Made from durable materials, adjustable hose guides provide reliable performance under frequent adjustments. Their adaptability ensures efficient operation and enhanced safety in diverse settings.
2.3 Retractable Hose Guides
Retractable hose guides are designed for applications requiring frequent adjustments or space-saving solutions. These guides feature mechanisms that allow hoses to extend and retract smoothly, reducing tangling and damage. Often used in automotive and industrial settings, they provide flexibility and durability. Constructed from robust materials like metals or high-strength plastics, retractable guides ensure reliable performance under varying conditions. Their compact design makes them ideal for tight spaces, enhancing efficiency and safety in dynamic environments. These guides are a practical choice for systems needing adaptability and ease of use. Their versatility ensures optimal functionality across multiple industries.
Materials Used for Hose Guides
Hose guides are made from metals, plastics, or composite materials, each offering durability, flexibility, and resistance to environmental factors, ensuring reliable performance in diverse applications.
3.1 Metals
Metal hose guides are highly durable and resistant to wear, making them ideal for demanding environments. Stainless steel, aluminum, and bronze are commonly used, offering excellent strength and corrosion resistance. These materials ensure longevity and reliability in industrial applications, where hoses are exposed to harsh conditions. Metals are preferred for their ability to withstand high temperatures and heavy-duty use, making them a critical choice for maintaining operational efficiency and safety in various machinery and systems.
3.2 Plastics
Plastic hose guides are lightweight, corrosion-resistant, and ideal for applications where flexibility and durability are key. Made from materials like PVC, nylon, or polypropylene, they offer excellent resistance to chemicals and abrasion. Plastics are often preferred in environments where metal components might corrode or react with substances. Their smooth surfaces reduce friction, minimizing wear on hoses and ensuring smooth operation. Plastic guides are also cost-effective and easy to install, making them a popular choice for lightweight and non-industrial applications where strength and versatility are required.
3.3 Composite Materials
Composite materials are engineered to combine the benefits of different substances, offering enhanced strength, durability, and resistance to environmental factors. These materials are often used in high-performance applications, blending properties like lightweight construction with superior thermal stability. Composites are resistant to corrosion and chemicals, making them ideal for harsh environments. Their versatility allows customization for specific industrial needs, ensuring optimal performance. Composite hose guides are particularly favored in aerospace and automotive industries due to their ability to withstand extreme conditions while maintaining structural integrity, making them a modern solution for demanding applications where traditional materials may fall short.
Manufacturing Process
The manufacturing process involves modern techniques, material selection, assembly, and rigorous testing to ensure durability and performance. Each step is critical for reliable hose guides.
4.1 Design Considerations
Design considerations for hose guides focus on material selection, operating conditions, and ergonomics. Factors like temperature, chemical exposure, and environmental factors are evaluated to ensure durability. The design must align with the hose’s flexibility and movement requirements, while also considering ease of installation and maintenance. Customization options, such as adjustable or fixed models, are tailored to specific applications. The goal is to create a user-friendly, efficient, and reliable component that meets industry standards and enhances system performance.
4.2 Production Techniques
Production techniques for hose guides involve precision machining and molding to ensure durability and customization. CNC machining is commonly used for metal guides, offering high accuracy. Injection molding is preferred for plastic components, allowing for complex geometries. Composite materials are fabricated using specialized processes like layup or 3D printing. Welding and assembly techniques are employed to integrate components seamlessly. Quality control measures, such as dimensional inspections, ensure compliance with industry standards. Surface treatments like coatings or anodizing enhance corrosion resistance and longevity.
4.3 Quality Control
Quality control in hose guide production ensures reliability and performance. Rigorous inspections are conducted to verify material integrity, dimensional accuracy, and surface finish. Performance testing under various conditions, such as extreme temperatures and pressures, validates durability. Certifications and compliance with industry standards are verified. A dedicated QA team reviews manufacturing processes to identify and correct defects. Traceability of components is maintained for accountability. Regular audits and customer feedback further refine quality benchmarks, ensuring consistent and superior products.
Applications of Hose Guides
Hose guides are widely used in industrial machinery, agricultural equipment, firefighting systems, and automotive applications to protect hoses from abrasion, kinking, and damage, ensuring efficient fluid transfer.
5.1 Industrial Machinery
Hose guides play a critical role in industrial machinery by protecting hoses from abrasion, kinking, and damage caused by moving parts. They ensure proper hose alignment, preventing disruptions in fluid or gas transfer. In factories and manufacturing plants, hose guides are essential for maintaining operational efficiency and safety. They are commonly used in robotic arms, conveyor systems, and heavy-duty equipment, where hose durability is paramount. By minimizing wear and tear, hose guides contribute to reduced downtime and extended equipment lifespan, making them indispensable in industrial settings.
5.2 Agricultural Equipment
Hose guides are vital in agricultural equipment to protect hoses from damage caused by moving parts and harsh environments. They are commonly used in tractors, irrigation systems, and harvesters to ensure proper hose alignment and prevent kinking or abrasion. By maintaining hose integrity, they contribute to efficient fluid and hydraulic system operation. Durable materials and robust designs make hose guides essential for withstanding the rigors of farming, ensuring continuous operation and reducing maintenance needs in the field.
5.3 Firefighting Equipment
Hose guides play a critical role in firefighting equipment by preventing hose damage and ensuring proper water flow during emergencies. They are designed to withstand harsh conditions, such as high pressure and extreme temperatures. In fire trucks and hydrant systems, hose guides help maintain hose alignment, reducing the risk of kinking or abrasion. Their durable construction, often featuring heat-resistant materials, ensures reliability in critical situations. By protecting hoses, they contribute to the efficiency and safety of firefighting operations, minimizing downtime and ensuring consistent performance when lives are at stake.
5.4 Automotive Systems
Hose guides are integral to automotive systems, ensuring hoses remain secure and properly aligned. They prevent damage from abrasion, kinking, and excessive heat in engine compartments. Used for coolant, fuel, and brake lines, these guides enhance durability and maintain consistent fluid flow. Durable materials, such as nylon or metal, are often employed to withstand harsh under-hood conditions. By protecting critical hoses, guides contribute to vehicle reliability, safety, and optimal performance, minimizing the risk of system failures during operation.
Installation and Maintenance
Proper installation ensures hose guides are securely fastened and aligned. Regular maintenance involves inspecting for wear and cleaning debris to prevent obstruction and ensure optimal performance.
6.1 Installation Tips
For proper installation, ensure the hose guide is aligned with the hose’s intended path. Use appropriate tools to secure it firmly, avoiding over-tightening. Position it in a way that allows smooth hose movement without kinking or rubbing against surfaces. Ensure the guide is compatible with the hose material and system requirements. Follow manufacturer instructions for specific mounting techniques. Regularly inspect the area for potential obstructions or hazards. Proper installation ensures safe and efficient operation, preventing wear and tear on both the hose and guide.
6.2 Regular Maintenance
Regular maintenance of hose guides is crucial to ensure optimal performance and longevity. Inspect the guides for signs of wear, tear, or misalignment. Clean debris or dirt that may interfere with hose movement. Lubricate moving parts if applicable to maintain flexibility and reduce friction. Check for loose fasteners and tighten them as needed. Replace damaged or worn-out components promptly to prevent system downtime. Schedule periodic inspections to identify potential issues early. Proper upkeep ensures smooth operation, reduces the risk of hose damage, and maintains overall system efficiency.
6.3 Troubleshooting Common Issues
Common issues with hose guides include misalignment, wear, and blockages. Inspect the guides for signs of damage or debris buildup. If the hose is misaligned, adjust the guides to ensure proper positioning. Replace worn or damaged components promptly to prevent further issues. Clean the guides regularly to remove dirt or obstructions. Lubricate moving parts if necessary to maintain smooth operation. Addressing these problems early can prevent system downtime and extend the lifespan of both the guides and the hoses. Regular checks help identify and resolve issues before they escalate.
Safety Considerations
Safety is critical when handling hose guides to prevent accidents and ensure system integrity. Proper installation and adherence to safety standards are essential to avoid hazards and maintain operational reliability.
7.1 Hazards Associated with Improper Use
Improper use of hose guides can lead to significant risks, including hose whip, system damage, and operator injury. Misalignment or excessive stress on hoses may cause ruptures, potentially releasing hazardous materials. Additionally, poor installation can result in operational inefficiencies and increased wear on equipment, leading to premature failure. Environmental hazards, such as chemical spills, may also occur if hoses are not properly secured. Ensuring correct usage is vital to prevent accidents and maintain safe, reliable system performance across various industries.
7.2 Safety Standards and Regulations
Safety standards and regulations for hose guides are established to ensure reliable performance and minimize risks. Organizations like OSHA and ISO provide guidelines for material quality, durability, and operational limits. Compliance with these standards is crucial to prevent failures and ensure operator safety. Regular inspections and maintenance are often mandated to uphold these regulations. Adhering to these norms helps prevent accidents, protects equipment, and maintains operational efficiency across industries. Proper certification and testing of hose guides are also essential to meet safety benchmarks and industry expectations.
7.3 Best Practices for Safe Operation
Best practices for safe operation of hose guides involve regular inspections, proper installation, and adherence to manufacturer guidelines. Always ensure the guide is securely fastened to prevent movement during operation. Staff should be trained on correct usage and maintenance procedures. Regular lubrication of moving parts and timely replacement of worn components are essential. Keep the surrounding area clear of obstacles to avoid interference. Proper alignment of the hose within the guide minimizes wear and extends service life. Following these practices enhances safety, reduces downtime, and ensures optimal performance.
Accessories and Customization
Hose guides offer various accessories and customization options, such as optional attachments and tailored solutions, to enhance functionality and meet specific application requirements, ensuring optimal performance.
8.1 Additional Features
Hose guides often come with additional features to enhance functionality. These include mounting brackets for secure installation, adjustable brackets for flexibility, and swivel joints for precise hose alignment. Durable materials ensure long-term performance, while weather-resistant coatings protect against environmental factors. Some models offer quick-release mechanisms for easy maintenance and replacement. Customization options, such as interchangeable components, allow users to tailor the system to specific needs. These features collectively improve efficiency, reduce wear and tear, and ensure safe operation in diverse applications. They also contribute to extending the lifespan of both the hose and the guide system.
8.2 Customization Options
Hose guides can be customized to meet specific application requirements. Users can choose from various materials, sizes, and mounting styles to suit their needs. Adjustable angles and lengths allow for precise alignment in unique setups. Customization also includes specialized coatings for corrosion resistance or high-temperature environments. Additionally, some manufacturers offer bespoke designs tailored to particular industries or machinery. These options ensure optimal performance, durability, and compatibility, making hose guides adaptable to a wide range of operational demands and environmental conditions.
8.3 Compatibility with Other Systems
Hose guides are designed to integrate seamlessly with various systems, ensuring compatibility across different applications. Their universal mounting styles and adjustable designs allow them to fit into existing machinery without modification. Compatibility is further enhanced by standardized sizes and materials that align with industry norms. This adaptability ensures smooth operation and prevents potential issues like misalignment or wear. Whether in industrial, agricultural, or automotive settings, hose guides are engineered to work alongside other components, maintaining efficiency and reliability across diverse operational environments.
Environmental Factors
Environmental factors such as weather, chemicals, and temperature extremes affect the durability of hose guides in various environments. Proper resistant materials ensure the longevity.
9.1 Weather Resistance
Hose guides must withstand various weather conditions, including UV exposure, rain, and temperature fluctuations. Materials like plastics and composites are often chosen for their durability in outdoor environments. Weather-resistant designs prevent degradation from moisture and sunlight, ensuring long-term functionality. Proper sealing and protective coatings enhance resistance to corrosion and wear. By using weather-resistant materials, hose guides maintain their structural integrity and performance in harsh outdoor settings, minimizing the risk of failure due to environmental factors.
9.2 Chemical Exposure
Hose guides often face chemical exposure in industrial and agricultural settings, requiring materials that resist corrosion and degradation. Metals like stainless steel and plastics like PVC are commonly used for their chemical resistance. High-density polyethylene is another durable option, offering excellent resistance to harsh substances. Proper material selection ensures longevity, while protective coatings further enhance resistance. Regular maintenance, such as cleaning and inspecting for chemical damage, is crucial to maintain functionality and safety in environments with frequent chemical exposure.
9.3 Temperature Extremes
Hose guides must withstand extreme temperatures, which can affect their durability and performance. Materials like silicone, stainless steel, and high-temperature plastics are ideal for such conditions. In high-heat environments, heat-resistant coatings and insulation are applied to prevent degradation. In freezing temperatures, guides may require lubrication to maintain flexibility and prevent brittleness. Proper material selection and design considerations ensure hose guides function reliably in temperature ranges from -50°C to 250°C, minimizing the risk of failure in extreme conditions.
Future Trends and Innovations
Future trends in hose guides include advancements in nano-coatings for enhanced durability, integration with smart sensors for real-time monitoring, and the adoption of 3D printing for customized solutions.
10.1 Technological Advancements
Technological advancements are revolutionizing hose guides, with innovations like smart sensors for real-time monitoring and predictive maintenance. Materials science is driving lighter, corrosion-resistant designs, while 3D printing enables customized shapes. Automation enhances manufacturing precision, reducing costs. Energy-efficient designs minimize environmental impact, aligning with sustainability goals. These innovations ensure hose guides adapt to evolving industrial demands, offering improved durability, flexibility, and integration with modern systems. As technology progresses, hose guides will become integral to smarter, more efficient operations across industries.
10.2 Sustainable Materials
The shift toward sustainable materials in hose guides focuses on reducing environmental impact. Eco-friendly options like recycled metals, biodegradable plastics, and plant-based polymers are gaining traction. These materials minimize resource depletion and lower carbon footprints. Innovations in composite materials combine durability with sustainability, ensuring longevity while being environmentally responsible. Manufacturers are also exploring recycling programs to repurpose hose guide components, promoting a circular economy. Sustainable materials not only align with global environmental goals but also maintain high performance standards, making them a viable choice for modern applications.
10.3 Smart Hose Guide Systems
Smart hose guide systems integrate advanced technologies like sensors and IoT connectivity for real-time monitoring and automation. These systems optimize hose alignment and reduce wear by adjusting to dynamic conditions. Sensors detect misalignment, temperature changes, or excessive stress, triggering alerts or automatic corrections. IoT-enabled guides allow remote monitoring and control, enhancing operational efficiency. AI-driven algorithms predict potential failures, ensuring proactive maintenance. Smart systems not only improve performance but also reduce downtime and extend equipment lifespan, making them a cutting-edge solution for modern industries.
Hose guides are vital for efficient and safe hose management across industries. Their diverse types, materials, and smart innovations ensure optimal performance and durability in various applications.
11.1 Summary of Key Points
Hose guides are essential for directing and controlling hoses in various systems, ensuring proper alignment and minimizing wear. They enhance efficiency, safety, and durability across industries. Key features include durability, versatility, and adaptability to different environments. Materials like metals, plastics, and composites offer unique benefits. Applications span industrial machinery, agriculture, automotive systems, and firefighting. Proper installation, regular maintenance, and adherence to safety standards are crucial for optimal performance. Hose guides play a vital role in ensuring reliability and longevity in fluid and gas transfer systems.
11.2 Final Thoughts on Hose Guides
Hose guides are indispensable in enhancing the efficiency and safety of fluid and gas transfer systems. Their durability, versatility, and adaptability make them a cornerstone in various industries. With advancements in materials and customization, their applications continue to expand. As technology evolves, smart hose guide systems and sustainable materials will likely dominate future trends. Proper installation and maintenance remain key to ensuring longevity and reliability. Hose guides exemplify how a simple component can play a vital role in modern machinery and infrastructure, offering both functionality and adaptability.